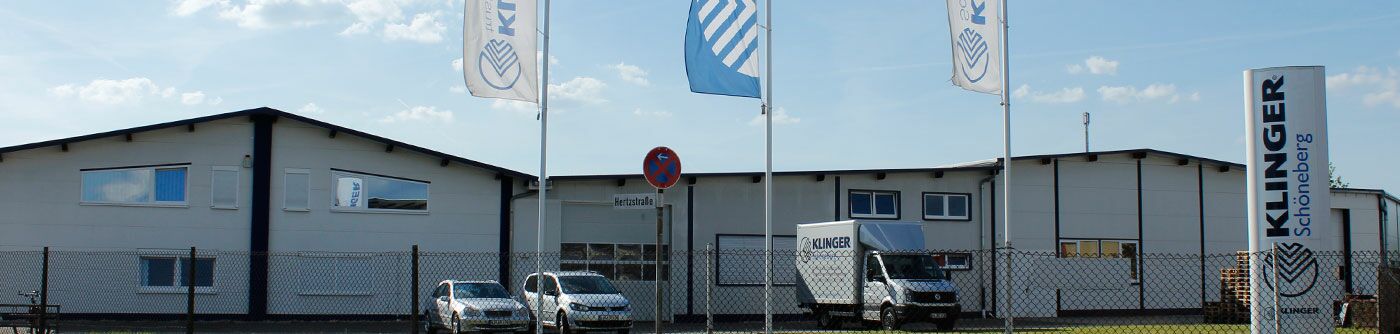
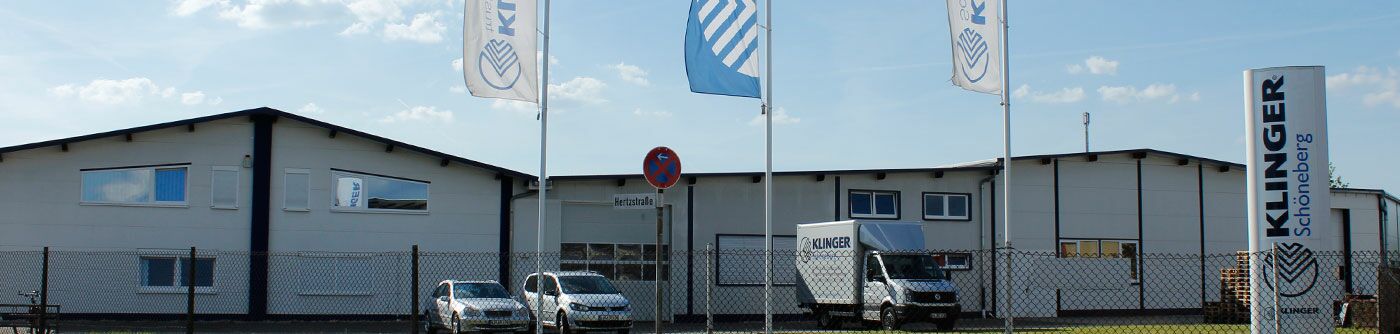
HISTORY OF KLINGER SCHÖNEBERG GMBH
Our History...
2024
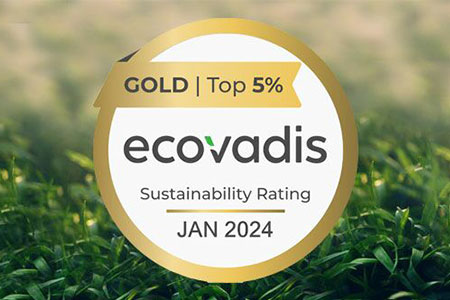
On April 1, 2024, Marcel Goßmann has taken over the management of KLINGER Schöneberg.
The previous Managing Director, Manfred Goßmann, who has been with KLINGER for over three decades, will retire on October 31, 2024.
KLINGER Schöneberg awarded EcoVadis Gold again: Through strategic sustainability management, a comprehensive supply chain risk analysis and the calculation of product and company carbon footprints, the EcoVadis assessment score was improved from 70 to 78 points.
2023
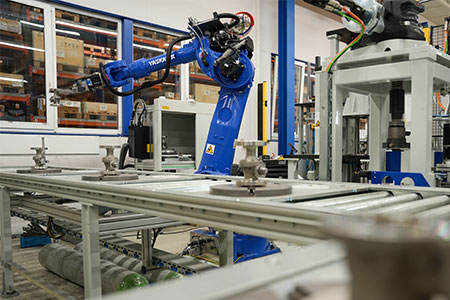
Our new semi-automated assembly line enables shorter cycle times, especially for high production volumes. By utilizing state-of-the-art robotics and automation, assembly, batch identification, testing, labeling, and material handling processes are optimized. The combination of human expertise and technology ensures flexible, cost-effective solutions and secures long-term competitiveness. Additionally, a conveyor-controlled transport system ensures a high level of autonomy in assembly automation.
2022
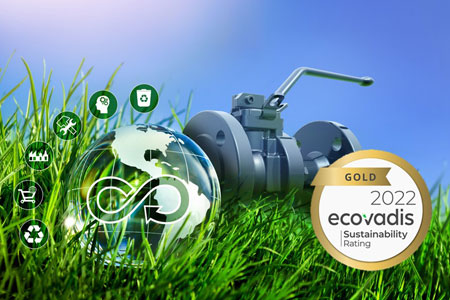
KLINGER Schöneberg has achieved the Gold rating for the first time in the EcoVadis sustainability assessment, which is based on 21 criteria across the categories of Environment, Sustainable Procurement, Ethics, and Labor & Human rights. Continuous improvement in all areas enabled us to convert our silver status from 2020 to gold in 2022 - placing KLINGER Schöneberg among the top 5% of all evaluated companies. One key factor in this success was sustainable procurement. In the environmental category, a circular economy process was introduced: In collaboration with a renowned recycling partner, we offer the chemical industry a closed-loop disposal system that ensures the proper recycling of industrial valves. This supports both ecological goals and the sustainable supply of raw materials. Thanks to green electricity, photovoltaics, and efficient technology, we have significantly reduced CO₂ emissions, as well as water and energy consumption. Ethics, labor, and human rights were also strengthened through the CSR report, which defines clear KPIs and objectives.
2020/2021
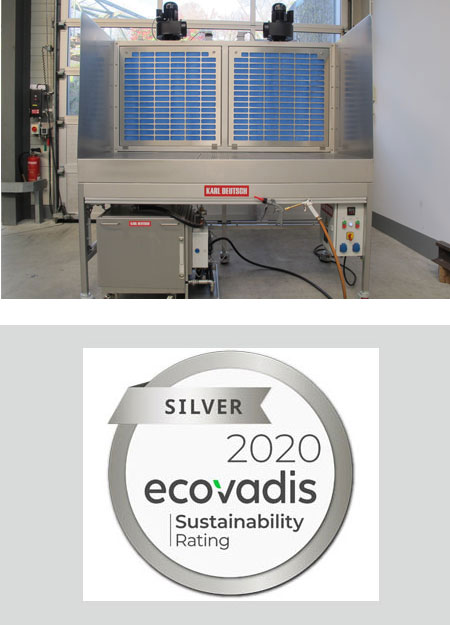
In 2020, we all had to learn how to deal with changes in our personal and business lives. No one could have guessed at the beginning of the year what challenges we would face as a result of COVID-19. Nevertheless, we managed to accompany our customers through this challenging time with our usual stability and reliability.
In order to expand research & development and to strengthen the innovation-promoting structures, the new building extension required for this purpose was completed. The new building and the state-of-the-art equipment will increase the company's innovative strength and speed up the time to market for new products. The department will continue to focus on targeted application-oriented research into new technologies and the timely development of innovative products in order to meet customer needs with the most advanced technologies and state-of-the-art solutions.
In addition, a new office for CAM programming has been built, as well as premises for the testing station for surface crack detection using the penetration testing method (system with extraction, washing water filter unit with UV disinfection including integrated water circuit and control system).
EcoVadis silver medal for KLINGER Schöneberg: Responsible behavior in the areas of environment, work practices, ethics and sustainability. Here it was shown that KLINGER Schöneberg was even able to increase its result from 2017. According to the current result, we are now in the top quarter of all evaluated companies and even better: among the top 8 percent in our own industry. This result is all the more remarkable as EcoVadis tightened up its criteria in the previous year and it was correspondingly more difficult to meet them.
2019
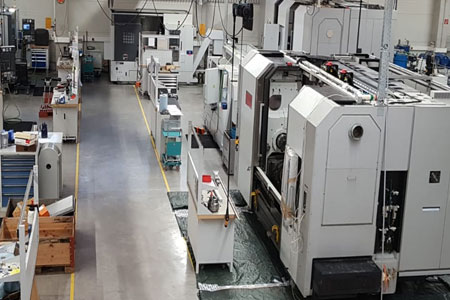
In the interest of a suitable and separate and last but not least representative design of the testing laboratory for the research and development department, we decided to build an additional extension onto the production hall. Now that the building permit and building permission have been granted, the planning and construction of the extension of approx. 215 m² to the production hall is in full swing. It is expected to be realised in the first half of 2020.
Based on the good experience and the resulting advantages in terms of efficiency, quality and throughput time, respectively the complete machining of parts in one clamping with our CNC turning/milling centre, make Mori Seiki, model NT5400 DCG/1800SZ, we have decided to purchase another CNC turning/milling centre, make Mori Seiki, model NT4250 DCG/1500SZ. This CNC machine follows the same concept and is only slightly smaller than the existing CNC machine. The reasons for the expansion of the machine park are to increase capacity and to relieve the milling machines (bottleneck machines) as well as to reduce external resources and improve delivery times.
Relaunch of the KLINGER Schöneberg homepage. Following intensive preparation, the contents were revised and the corporate design was implemented. In addition to the corporate design, the redesign also focused on adapting the contents to the needs of our target group, as well as the so-called Responsive Design. This gives our customers, partners or interested parties an even more detailed overview of KLINGER Schöneberg's core competences and range of services. As usual, the News section regularly reports on news, the company, products and events.
2018
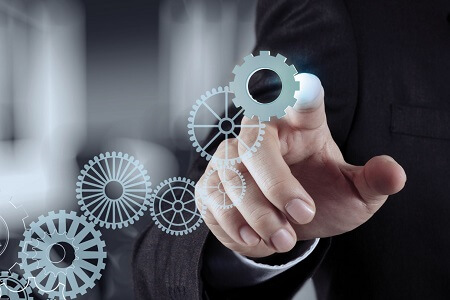
In order to promote and guarantee the continuity and quality of new, innovative products, the internal innovation-promoting structures are expanded even further. In this context, the "Research and Development" department will be more strongly positioned in terms of personnel and equipment by the end of 2019. This will enable the company to achieve greater innovative strength and faster "time to market" times for new products. The department will continue to focus on targeted application-oriented research into new technologies and the timely development of innovative products to meet customer needs with the most advanced technologies and state-of-the-art solutions. Furthermore, the quality standard within KLINGER Schöneberg can be further increased by the internal networking of the departments and the processing of the research and development results.
2017
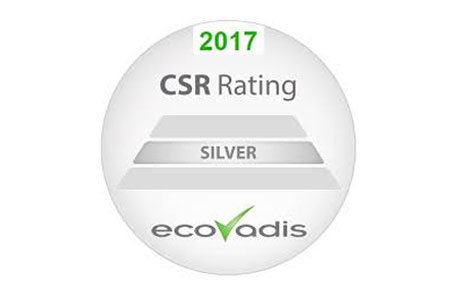
KLINGER Schöneberg has passed the first EcoVadis assessment and achieved a score of 56 points. This puts us well above the average for the industrial sector (42.2 points in October 2016). The result achieved is the status quo, which now needs to be continuously improved. Initial measures to this end have already been initiated. The majority of large companies are under enormous pressure from stakeholders demanding transparency in sustainability and CSR practices (voluntary corporate social responsibility), which also includes their supply chains. EcoVadis is a leading provider of sustainability and CSR assessments, and operates the first collaborative platform that enables companies to measure the sustainability performance of their suppliers. The sustainability performance of companies is assessed in four categories: Environment, labour practices, fair business practices and sustainable procurement. Each year, EcoVadis evaluates around 6,000 companies in a total of about 150 different industrial sectors in 95 countries. Around 100 large multinational companies, including many of our major customers, use EcoVadis to monitor and evaluate the sustainability performance of their suppliers.
2016
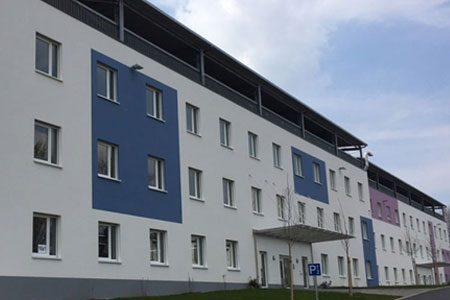
The steady growth and the positive development of business and the associated increase in sales and marketing staff necessitates an expansion of office space. We consequently moved into new offices. The new address is now in Waldems-Esch and only about 5 km away from Idstein. An office floor was rented in a building complex consisting of three units in House A1, Level 2 South. The office space comprises a total of 371 m² and has 7 offices, a meeting room, a project room, an air-conditioned server room, and a lounge area. This is the first time the office floor is occupied. The building is equipped with Cat7 cabling and a fibre optic cable connection.
A special assembly workstation has been set up to ensure efficient and effective assembly of our pneumatic MIG actuators. The facility consists of two assembly tables with changeover facilities for the different actuator sizes. Here, the components are exactly positioned and fixed for assembly. In addition, this ensures the continuous quality and functionality of the actuators.
In accordance with our corporate identity and group philosophy "One Group - One Brand", we contribute significantly to our value system based on "Global Regionality" with our uniform and worldwide corporate design in connection with the slogan "trusted.worldwide”. We are a regional partner for our shareholders and at the same time part of a global group. The corporate design has a high recognition value and presents a uniform, positive and unmistakable image to the public and internally.
2015
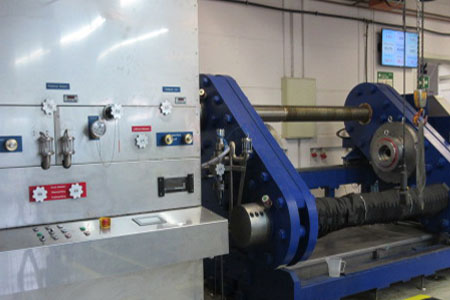
For strategic reasons, the business unit of KLINGER SCHÖNEBERG GmbH at the Brettorf location was outsourced to an independent company, KLINGER Convey GmbH, with effect from 01.01.2015. The aim of this move is to strengthen the company's position in its target industries and to focus on the development, production and sales of butterfly valves.
Purchase of a CNC turning/milling centre, make Mori Seiki, model NT5400DCG / 1800SZ including a 40-fold tool magazine. The advantages of the new CNC machine are that the parts are completely machined in one clamping. Compared to multi-machine CNC machining, this results in a significantly shorter machining time as well as significantly reduced throughput time. In addition, the machining accuracy is again significantly improved.
Acquisition of a new valve test bench for pressure and leak testing of valves of nominal widths DN100 up to and including DN500 and up to a pressure of 600 bar. Menu-guided Siemens control via touch screen and networked connection for direct recording and logging of the test results.
Due to increasing customer requirements and the resulting professional handling of the oil and grease-free assembly, a new assembly room has been set up especially for this purpose. The equipment ranges from a pressure test bench with demineralised water in an immersion basin and nitrogen as the test medium, to air conditioning with a special filter, ultrasonic cleaning bath, transport trolley, film sealing device and a UV lamp with black light. The room may only be entered with appropriate protective clothing.
2014
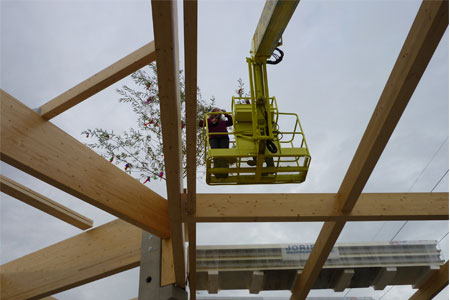
Expansion of the storage area in Graben-Neudorf by adding another warehouse. Adjacent to and in connection with our existing central warehouse, we were able to put another warehouse with approx. 260 m² and 300 pallet spaces into operation. By expanding the storage capacity, we are also logistically reacting to the growing demand.
2013
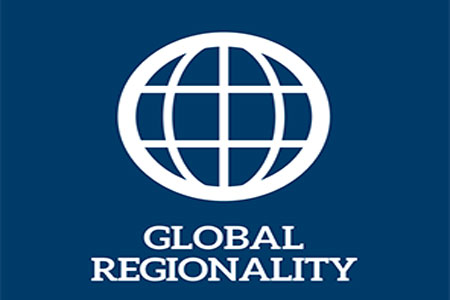
The representative office of KLINGER Schöneberg which has been operated and established since 2006 and is based in Shanghai, was dissolved as of 01.01.2013 and transferred to the newly founded company of KLINGER Shanghai Ltd. (Wholly Foreign Owned Enterprise). This change of strategy reflects the fact that the different tasks and business areas are no longer handled in different units, but coordinated and integrated in one company. This reorganisation and the associated merger generate not only stronger competencies but also cross-selling effects to acquire new customers and markets for the products and services of industrial valves and industrial seals and facilitates offering them to a broader target group. The previous contact persons remain unchanged.
2012
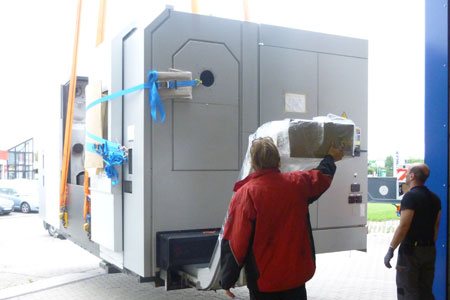
At the Brettorf site, an expansion program was carried out as part of the modernisation and capacity expansion of the in-house production facilities with the aim of broadening the product portfolio and permanently securing the quality of our high-performance butterfly valves. The core of this program was the purchase of a CNC machining centre, make ENSHU, model GE590H with a FANUC F-31iM control, a pallet changer system and a 40-fold automatic tool changer. The total weight of the machine is 22 tons. With this CNC-machining centre, it is now possible to manufacture butterfly valves up to and including the size DN600.
2011
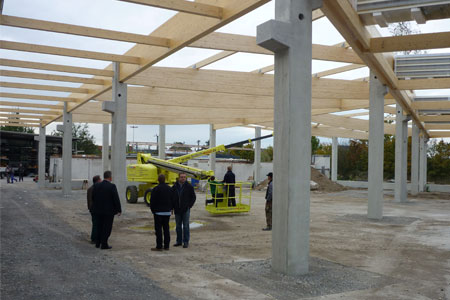
KLINGER SCHÖNEBERG GmbH further expands its business activities and competences in the field of 90° valves by merging with Convey Flow Control GmbH based in Brettorf on 01.01.2011. The product portfolio of high-performance butterfly valves perfectly complements the high quality INTEC system technology of ball valves for the process industry. At the site in Brettorf, KLINGER SCHÖNEBERG GmbH continues to develop butterfly valves independently and at the same time benefits from the internationality of the KLINGER Group.
In the same year the expansion of the production and building area in Graben-Neudorf was realized by adding another production hall. Adjacent to our existing building areas we were able to put into operation a production hall with an additional 1,500 m². We will use this production hall to expand our mechanical processing efficiently and in line with the latest state of the art. With the expansion, we are acting on the good company development and can therefore react quickly and flexibly to the requirements of our customers.
2010
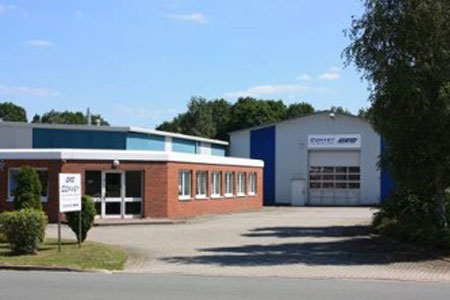
As of January 1, 2010 the shares of Convey Flow Control GmbH based in Brettorf were taken over by KLINGER Holding Deutschland GmbH. In the further course of the transaction, the business operations of Convey Flow Control GmbH are integrated into KLINGER SCHÖNEBERG GmbH through an asset deal. Convey Flow Control GmbH is a manufacturer of double eccentric metal and soft-seated butterfly valves and extends the product portfolio of 90-degree valves. Manfred Goßmann has been assigned the company management.
2009
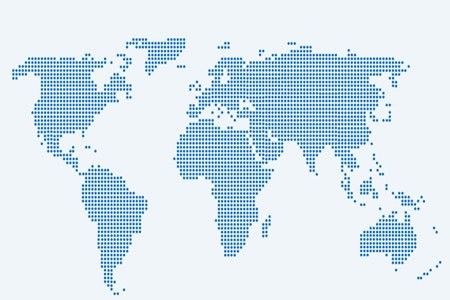
The previous CEO Michael Wüllerich leaves the company on 01.01.2009. He will work exclusively for the company as a legally independent consultant. On this basis, he intends to use his many years of sales experience to develop new market potential and expand existing marketing structures in the Far East contract area (South/East Asia and China). He will be supported in this endeavour by using the company's own resources.
2006
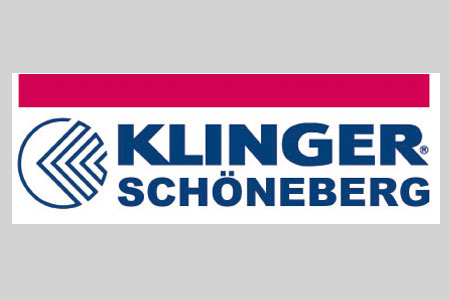
Foundation of KLINGER SCHÖNEBERG GmbH, located in Graben-Neudorf, through the merger of TEG-SCHÖNEBERG GmbH with the industrial valves division of KLINGER GmbH, under the management of Manfred Goßmann and Michael Wüllerich. The valves warehouse from Idstein is physically concentrated in a newly built central warehouse in Graben-Neudorf. The sales team remains in the traditional site in Idstein. The merger of the two companies follows a consistent move to meet the wishes and requirements of customers for a comprehensive range of services under the philosophy "Connect with Quality". The expanded range of services results in an outstanding performance spectrum for customers, from qualified consulting and highly developed series products to customised solutions.
In the same year, KLINGER SCHÖNEBERG GmbH opens its own registered representative office in Shanghai, thus continuing its drive towards internationalisation. The representative office is a logical and consequent step in order to guarantee individual consulting and support for the international and globally operating customers in the region.
2002
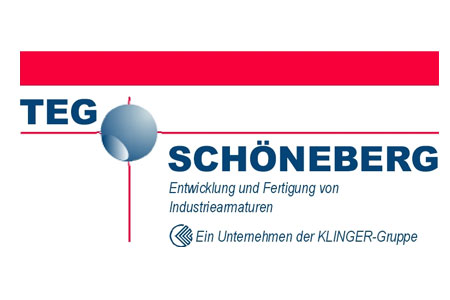
In the course of the retirement succession plan, TEG-SCHÖNEBERG GmbH is taken over by KLINGER GmbH, thus becoming a member of the globally operating KLINGER Group.
TEG-SCHÖNEBERG GmbH remains an independent company within the KLINGER Group, which assures customer requirements in close cooperation with KLINGER GmbH in Idstein.
2001
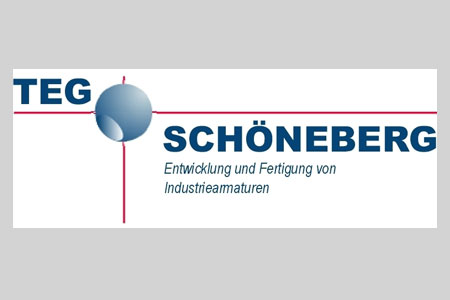
Company merger between TEG mbH and Schöneberg OHG. The result was the TEG-SCHÖNEBERG GmbH & Co. KG with CEO’s Gerd Kraft and Peter Schöneberg. The direct sales business was intensified through Mr. Schöneberg, a businessman with many years of experience and particularly strong market and customer competence. With the founding of TEG-SCHÖNEBERG GmbH, the financial year provided the opportunity to implement its transformation from developer to innovative manufacturer. With now three core competencies in development, production and sales, TEG-SCHÖNEBERG GmbH is a supplier that consistently focuses on the needs of its customers. Positioning of innovative products under the "INTEC" label as a one-stop supplier of ball valve system technology.
1993 - 1999
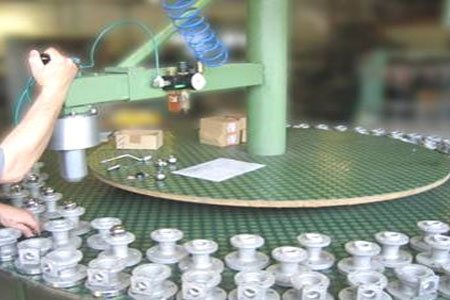
The existing value chain is expanded with the move into a newly constructed building comprising offices and a production hall. Now the prototypes of innovative industrial valves developed and manufactured by the design engineers can be systematically implemented up to series production using modern inspection and test benches. The range of services is very positively received by the customers and TEG mbH strengthens the mechanical production sector and establishes the series assembly sector. The market rewards the strategy of receiving integrated developments and detailed designs, tested prototypes up to series production readiness and feasibility studies including cost analysis from one single source.
1993
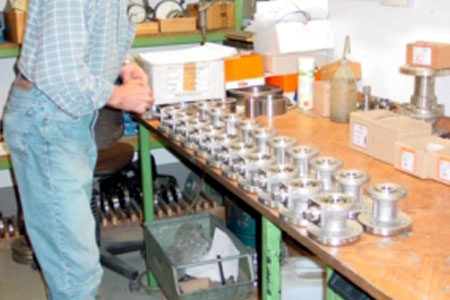
Gerd Kraft founds the technical development company, TEG mbH, as a consulting company for valve development. The founder of the company, a developer of industrial valves - in particular of ball valves for industrial applications with many years of experience - operated in the founding years of the company with few but very efficiently working human resources.