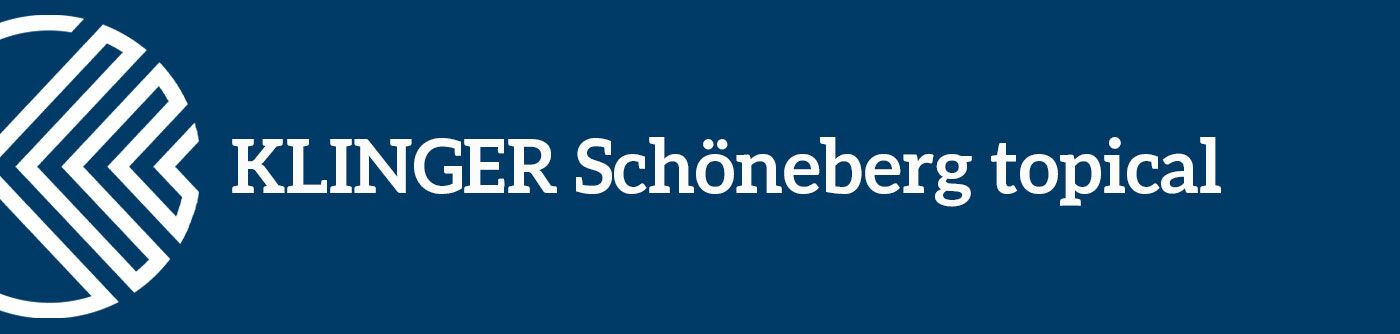
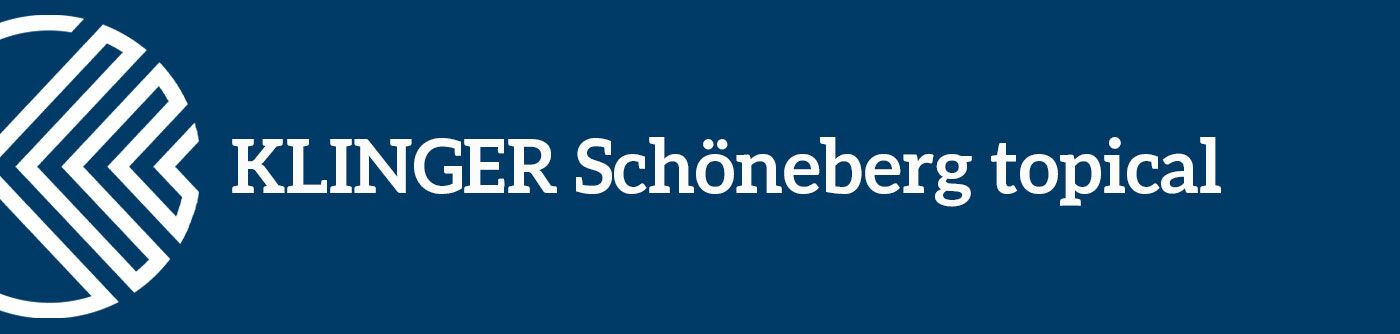
Ball Valves for High-Pressure Hydrogen Applications
For more than a century, hydrogen has played a crucial role as a raw material for various applications. Globally, approximately 94 million tons of hydrogen are consumed annually, with a rising trend.
Refineries (hydro treatment processes, cracking, etc.) and the chemical industry (ammonia and methanol production, food chemistry, synthesis, etc.) account for the largest share of this usage. Due to the changing policies towards decarbonizing the energy sector, hydrogen as an energy carrier, ideally produced with low CO2 emission methods, is increasingly in focus. In addition to industrial use in chemistry, petrochemistry, and refining, future applications focus on the steel industry, fuel cell mobility, as well as stationary and mobile applications.
Hydrogen-compatible ball valves
The application possibilities are as diverse as the valves required for hydrogen production, storage, and transport. The valves used along the hydrogen value chain must meet stringent safety, design, material resistance, and quality requirements, not least because hydrogen, as the lightest element, is highly diffusive. Furthermore, the valves must withstand extreme pressures and temperature ranges.
For shut-off in the high-pressure range (120 bar) of hydrogen supply, the three-piece ball valve INTEC 113G (K811)-M-S-HP-FSD is used in nominal size NPS 2” and with the Class 2500 pressure rating.
- These valves have high-precision-bearings with a spring-loaded metal-to-metal seating surface at both ends.
- The stem, ball, and bearing trunnion are one piece made of super duplex material.
- The ball and ball seats have a pore-free, nickel-based hard alloy coating applied by thermal spraying with subsequent melting. The ball and seat system has a surface hardness of 62 HRC and is lapped. This results in a permanent, gas-tight shut-off in the port and ensures maintenance-free operation even in applications with high switching cycles.
- The design of the trunnion-mounted ball valve ensures that the extreme forces resulting from the high pressure are absorbed by the stem and bearing trunnion, resulting in significantly lower operating torque. This leads to significant cost savings in selecting the actuator.
- The body material, of 316L (austenitic steel), meets the generally accepted criteria for handling hydrogen, as confirmed in a position paper by the German Engineering Federation (VDMA).
- The ball valve can be equipped with extensive accessories, such as a stem extension, a manual gearbox, and more.

The INTEC 113G (K811)-M-S-HP-FSD three-piece ball valve is the right choice for high-pressure hydrogen applications.
As a specialist in industrial valves, KLINGER SCHÖNEBERG GmbH sets high standards for the design and material selection of the individual valve components to ensure permanent technical tightness in the port and to the outside. “To design our valves, we use our own dedicated analysis and design tool, CHOICE INTEC, with which we develop a cost-effective, functionally optimized solution,” says Marcel Goßmann, Managing Director of KLINGER Schöneberg.
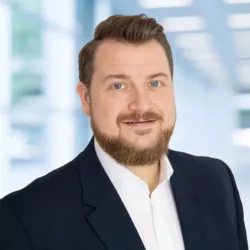
"As well as the overall process, investment and operating costs, and energy requirements, we also consider the technical environment.“
Marcel Goßmann, Managing Director of KLINGER Schöneberg
The use of reliable, high-quality shut-off valves from the INTEC series guarantees the safe and efficient handling of hydrogen. Thanks to ongoing technical development, the importance of reliable and safe components for hydrogen applications will continue to increase.