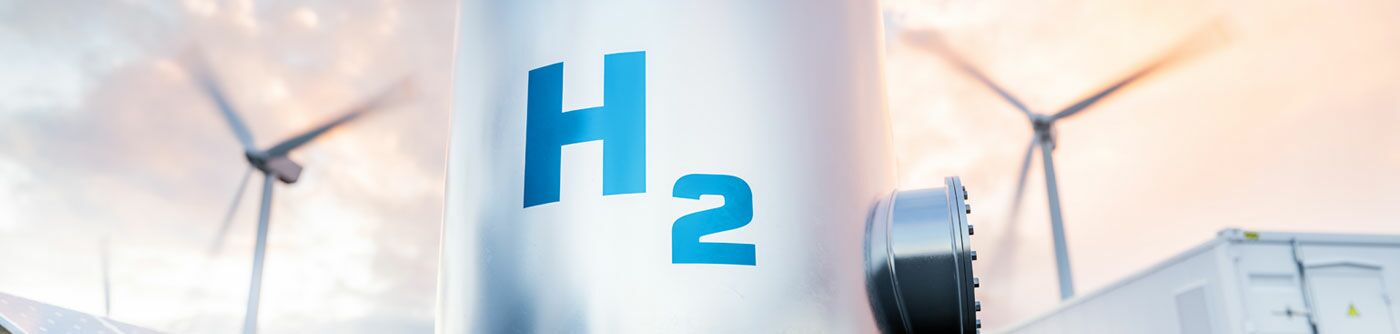
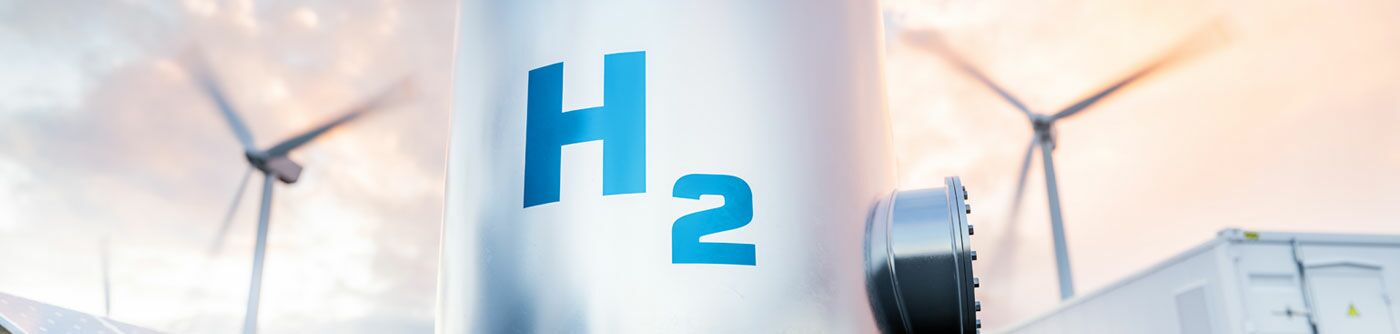
Hydrogen in Elektrolysis
Power to Valve for green hydrogen.
Process description
Hydrogen can be produced in large quantities by electrolysis without CO2 using energy from renewable sources.
In large-scale production, ordinary demineralized water is split into oxygen and hydrogen by means of electric current in an electrolyzer.
Commercial water electrolysis systems for industrial use are currently designed as alkaline electrolysis with the electrolyte potassium hydroxide or as membrane electrolysis "Proton Exchange Membrane (PEM) Electrolysis" with a proton conducting polymer membrane. In alkaline electrolysis, valves are also used to handle the aqueous electrolyte solution.
Currently, electrolysis plants are largely operated at atmospheric pressure. In principle, increasing the operating pressure has the advantage that the hydrogen produced at high pressure does not have to be recompressed as much for storage purposes, which results in potential energy savings.
Requirements
-
Alkaline electrolysis at approx. 90°C and an operating pressure between atmospheric and 120 bar (commercially up to approx. 30 bar).
-
Membrane electrolysis at approx. 90°C and an operating pressure of 350 bar.
-
High requirement for tightness - gas tightness at high pressures.
-
Safety of the valve.
-
High demands on pressure-bearing materials to avoid hydrogen-induced stress corrosion cracking.
-
Long service life even at high pressures.
Solutions
The electrolysis processes for hydrogen production, including water treatment, cooling, hydrogen purification and the generation of high-purity hydrogen, require reliable and safe valves from KLINGER Schöneberg.
INTEC K200 - two-piece flanged ball valves
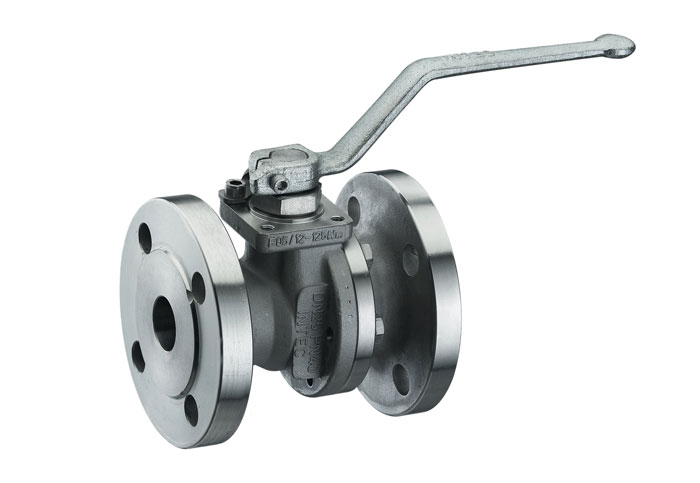
Proven design with perfect technical functionality. The ball valves are available in various material combinations and with different features.
INTEC K200 - floating ball, soft seated
INTEC K204 - floating ball, PEEK seated
INTEK K220 - floating ball, soft seated, single side spring loaded seat ring
INTEC K210 - trunnion mounted ball, soft seated, both sides spring loaded seat rings
INTEC K224 - floating ball, PEEK seated, single side spring loaded seat ring
INTEC K214 - trunnion mounted ball, PEEK seated, both sides spring loaded seat rings
INTEC K211 - trunnion mounted ball, metal seated, both sides spring loaded set rings
INTEC K221 - floating ball, metal seated, single side spring loaded seat ring
INTEC K811 - three piece high-pressure ball valve

High precision bearings and both sides spring loaded seat ring elements are responsible for safety handling in all applications of the high-pressure ranges.
INTEC K811 - trunnion mounted ball, metal seated, both sides spring loaded seat rings
..
Happy to provide you with further information
- Marcel Gossmann, Business Development Manager / Management Assistent
+49 6126 950 - 268 marcel.gossmann@klinger-schoeneberg.de