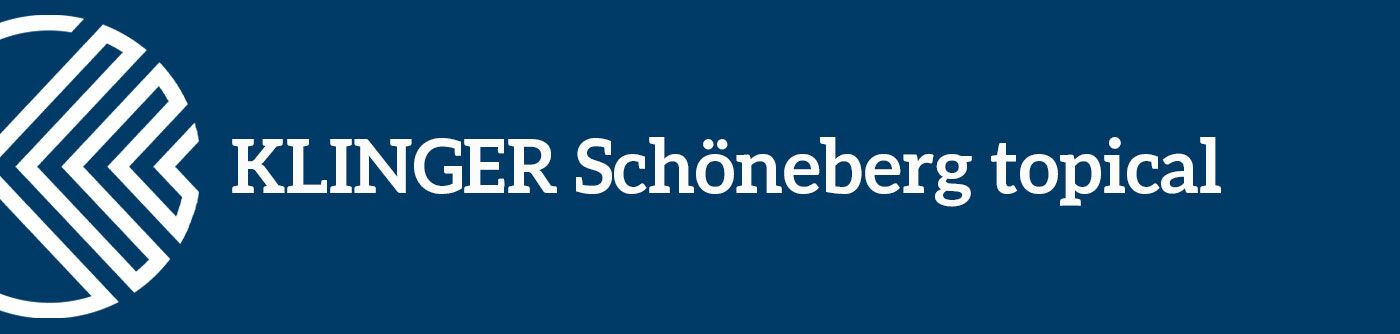
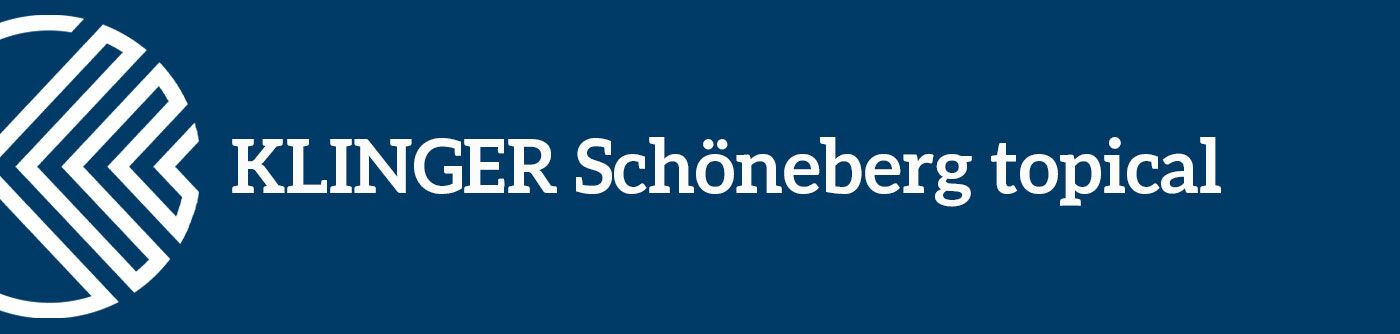
Hydrogen refueling stations
Dive into the challenges of refueling hydrogen-powered trains
How to refuel hydrogen fuel cell trains? Learn about the unique challenges and how reliable KLINGER Schöneberg’s INTEC ball valves can help overcome them.
The world's largest hydrogen-powered train has been running in Hesse, Germany, since 2022, marking a significant milestone in sustainable transportation. Hydrogen fuel cells offer a cleaner alternative to traditional diesel engines, emitting only water and steam, and can accelerate the 160 seats offered per vehicle to up to 87 mph (140 km/h). However, the transportation and storage of hydrogen come with its unique set of challenges, including the need for reliable and safe equipment to handle hydrogen.
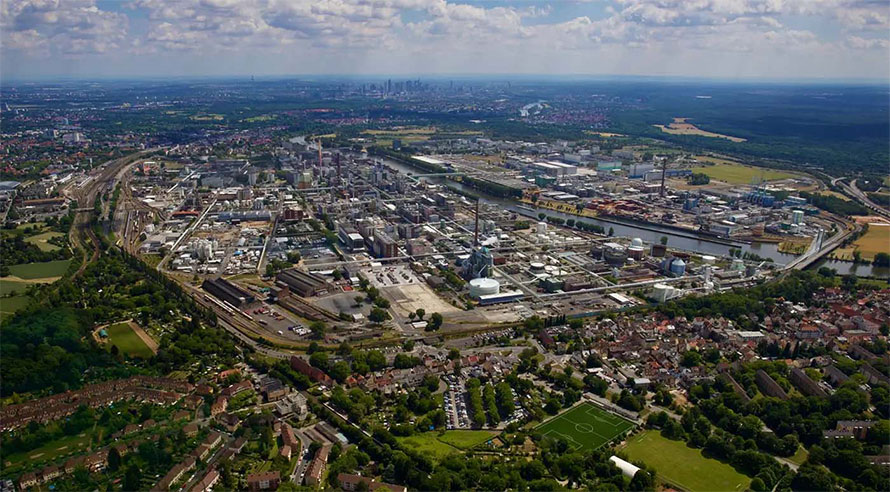
The starting point: Industrial Park Höchst in Hesse, Germany. Copyright: 2021 Infraserv GmbH & Co. Höchst KG
In 3 steps to the refueling station
As part of the lighthouse project for refueling stations for fuel cell trains, high-quality and durable shut-off valves are required to ensure safe and efficient operation during a three-part process:
- The necessary amounts of hydrogen are generated from various chemical production processes as a byproduct and an additional electrolyzer.
- The hydrogen is then distributed through the pipeline network for storage and ultimately for refueling.
- By using compressors, the hydrogen is compressed to a high pressure to efficiently store it for use in fuel cells or combustion engines.
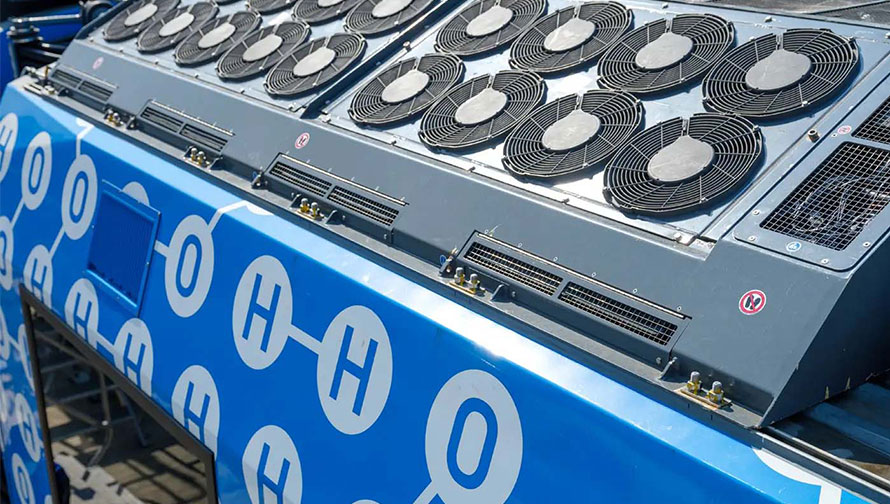
The fuel cell on the hydrogen-powered train in Hessen, Germany. One hydrogen filling lasts for 1,000 km.
Copyright: ALSTOM SA 2021, Christoph Busse, Coradia iLintT.
The significance of ball valves in hydrogen refueling stations for fuel cell trains
In the process of refueling fuel cell trains with hydrogen, ball valves play a crucial role as a critical component. High pressure is necessary for efficient hydrogen storage, which is achieved through the utilization of compressors. Ball valves ensure that the hydrogen is compressed to 500 bar at the compressor inlet with an intake pressure of 7 bar. For the proper handling of hydrogen, it is necessary to use valves of high quality that have been demonstrated to be effective in the process.
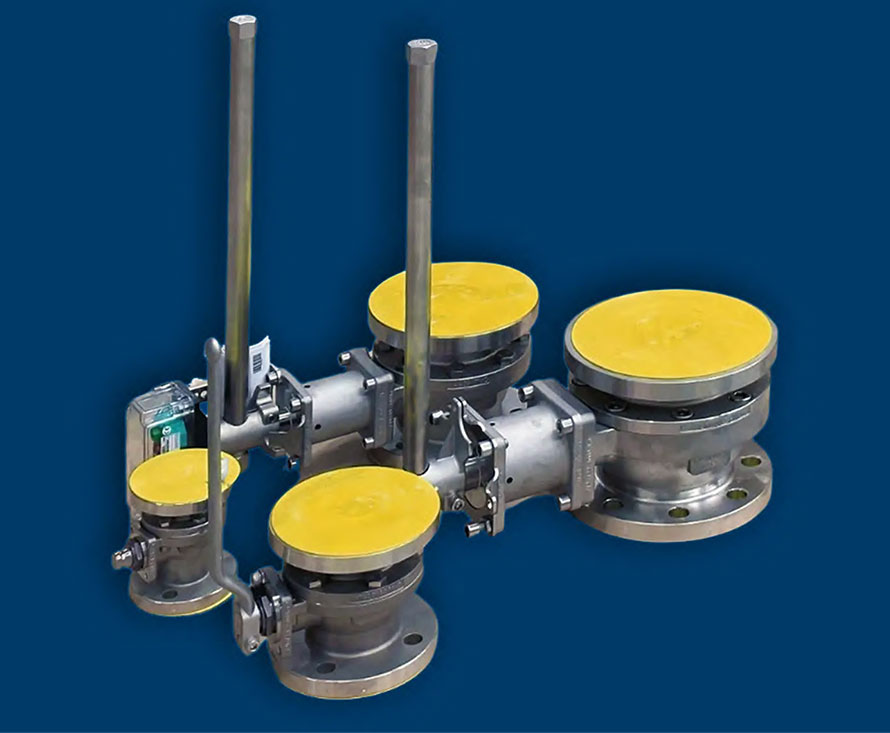
The INTEC K200-S-FS by KLINGER Schöneberg is a two-piece ball valve with flanges according to EN 1092.
Valves for hydrogen refueling stations
To meet these challenges, KLINGER Schöneberg ball valves with exceptional material quality, safety, and leak-tightness are essential. The INTEC K200-S-FS ball valve from KLINGER Schöneberg is now one of the products being used in the hydrogen refueling process.
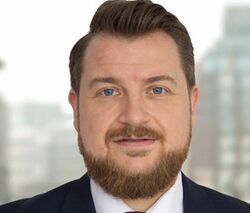
The installed INTEC K200-S-FS ball valves in the sizes DN50 to DN100 are ideal for this hydrogen application, ensuring to limit leakage, and thus minimizing fugitive emissions.
Marcel Goßmann, Business Development Manager at KLINGER Schöneberg, sees great potential for INTEC valves in hydrogen applications.
The use of high-quality, reliable shut-off valves like the INTEC series is critical to ensure the safe and efficient operation of hydrogen. With ongoing technological advances and increasing demand for green transportation, the importance of reliable and safe equipment for hydrogen handling will continue to grow.
Frequently asked questions (FAQ)
- What type of valves are being used in the hydrogen refueling process?
INTEC ball valves from KLINGER Schöneberg with exceptional material quality, safety, and leak-tightness are being used in the hydrogen refueling process for the lighthouse project. The INTEC K200-S-FS ball valve from KLINGER Schöneberg is one of the products being used. - How do fuel cell traction units work?
Fuel cell traction units are local emission-free trains that have a hydrogen tank and a fuel cell on the roof. The fuel cell converts hydrogen and air into water, generating electricity that charges the on-board lithium batteries and drives the electric motor. The trains emit water vapor instead of CO2 and other combustion gases. The train also carries a battery that temporarily stores the electrical energy generated on board and recovers braking energy, also known as recuperation. These trains can travel up to 1,000 kilometers on a full tank of fuel and can reach speeds of up to 140 kilometers per hour. The hydrogen tank system in each vehicle consists of two tanks with a capacity of approximately 130 kg each and a nominal pressure of 350 bar.
Your contact
- Marcel Gossmann, Business Development Manager / Management Assistent
+49 6126 950 - 268 marcel.gossmann@klinger-schoeneberg.de